181 Speaks with Jill Lonergan & Chris Conrad of Level 10 Construction
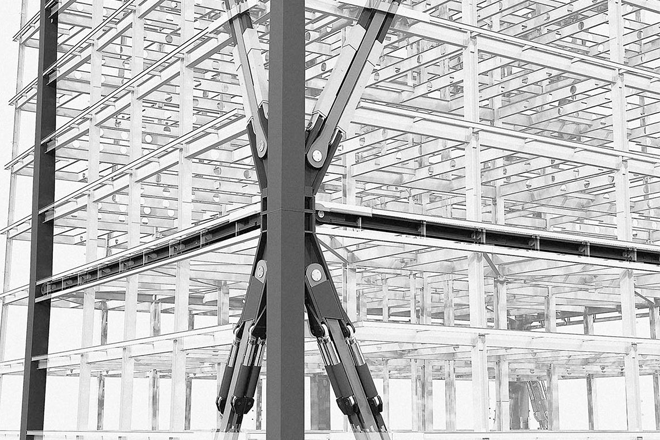
Even with our 21st-century daily familiarity with skyscrapers that touch the sky, we look up and wonder: how is it possible to build this? Level 10 Construction looks at a blueprint and asks another question: how can we achieve this in such a way that we exceed all expectations of completion, quality, and safety? How can we not only build something great, but something exquisitely crafted that takes what we thought was possible and pushes it beyond that limit?
What Level 10 brings to the construction of 181 Fremont is a model of how brilliant design and construction can take next-level dreams and make reality exceed them. Here we speak with Jill Lonergan, Level 10’s NorCal Marketing Director, and Senior Project Manager Chris Conrad about Level 10 and the construction of 181 Fremont.
Jill Lonergan, NorCal Marketing Director
What are some of the most notable projects Level 10 has worked on?
Level 10 has completed projects for the Moffett Place Campus, Moffett Towers II Campus, Facebook MPK 20, Central & Wolfe, HGST South Bay Initiative, SilevoSolar California Technology Center, K3 in San Diego, and the San Diego Museum of Contemporary Art renovation.
What sets Level 10 apart from other construction firms? How are these differences evident in the building of 181 Fremont?
Innovation. Safety. An outstanding example of both is the cantilevered safety net that Senior Superintendent Chris Wilcox designed and had installed above an adjacent (and historic) brick building with a childcare playground on the roof. The 181 Fremont team met with GLL Real Estate Partners, the owners of the adjacent building, to recommend and highlight the plans for a $1.5 million safety netting system to be installed to protect the children and staff from falling debris. A handful of concerns were expressed by the daycare program and GLL, including disruption of daily activities and the obstruction of daylight. All concerns were addressed, and the final design of the system was approved.
During this phase, the 181 Fremont team met with the daycare managers continuously to insure they were kept in the loop and were able to address any issues with the netting design and future installation. At this point, we performed a drop test to evaluate and adjust retention. Once design and installation were approved for the safety net system, it was critical to test its load capacity. For this test, Level 10 built a mock-up of the system on a heavy-duty scaffolding structure that would eventually be installed over the playground. Four-hundred-pound sand bags were dropped at increments of 25 feet while readings were taken to study how the netting took the load. (You can see our drop test video here: http://bit.ly/2xVyJrX.)
Another vital factor in how we work is building relationships. Level 10 has maintained strong neighborhood relations throughout the life of this technically complex project.
What’s unique about the design and construction of 181 Fremont that people might not realize at first?Building 181 Fremont actually presented some uniquely challenging logistics which required intensive pre-task planning; coordination of the multiple subcontractors; and site-specific safety requirements.
We also had to contend with the challenge of creating below-grade (underground) parking. The 181 Fremont team constructed deep below-grade parking, and this required a thorough understanding of the area’s soil and water table conditions.
Another factor that was unique on this project was the way it required strong communication with local agencies. The 181 Fremont team worked closely with a multitude of city and county inspectors and agencies, including Muni, PG&E, SF Department of Public Works, SF Planning & Building Department, SF Fire Marshal, SF Health Department, and, of huge importance, the Transbay Joint Powers Authority. Our ability to build strong relationships with these agencies allowed us to quickly and efficiently secure the necessary approvals and permits for the project.
Chris Conrad, Senior Project Manager
How central is the question of resilience and seismic activity to your building practice—and to building 181 Fremont in particular?
181 Fremont falls under 2010 building codes, which incorporated a higher safety standard as a result of the World Trade Center collapses and the lessons learned from the San Francisco and Northridge earthquakes. Specifically, 181 Fremont has shock absorbers to compensate for lateral stability and sway.
What is the current status of construction on 181 Fremont? Which elements are the last to take shape?
181 Fremont is nearing all its city agencies’ inspections for the core and shell structure. Following this milestone, the residential units have monthly turnover dates through the end of May 2018. A confidential technology client recently signed a lease for the entire commercial space, and the complete buildout will extend beyond this date and is currently under development.
How closely did Level 10 collaborate and coordinate with the architects at Heller Manus and the design firm ODADA, the structural engineering firm Arup, the MEP engineering firm WSP, and the Transbay Transit Center?
Daily coordination with each of these entities occurs either formally or informally. As critical partners in this building’s success, all parties collaborate for its successful completion.